The world of cutting and shaping metal is wide open with possibilities. Choosing a metal for a machining project isn’t as simple as just grabbing any available piece of material.
So, which metal is right for you? Explore the six best metals for machining in this guide.
1. Steel
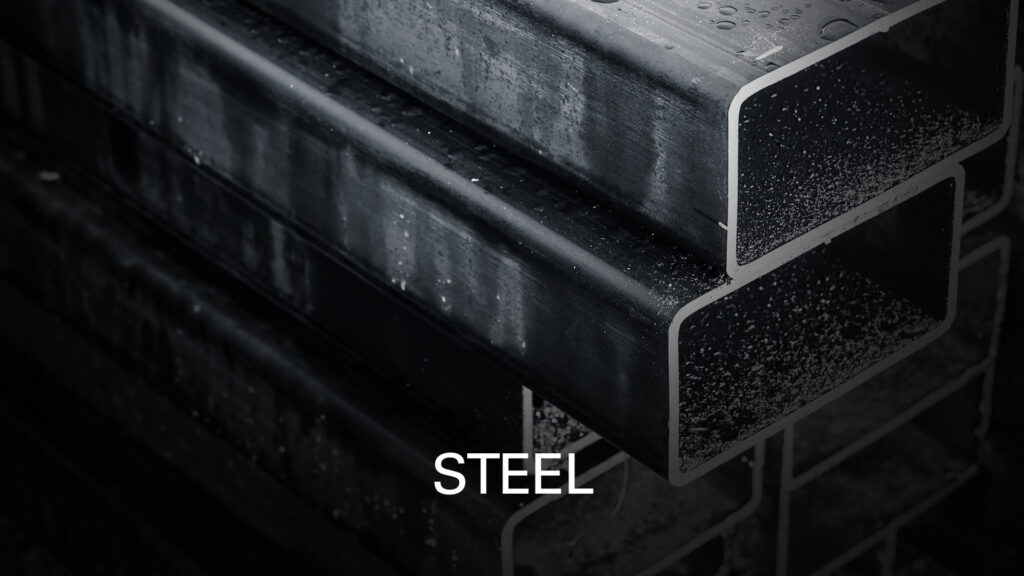
Steel—a metal alloy of iron and carbon—is no. 1 here with good reason. It’s the most popular metal for machining because it’s versatile, strong, and among the easiest materials to machine. It’s also affordable compared to some other metals, so it’s a good choice for almost any project or beginners learning to operate the machine.
Pros:
- Strength – Can withstand a lot of wear and tear.
- Durability – Can last for many years.
- Versatility – Can be used to make a wide variety of parts.
- Affordability – Comes at lower costs than other metals we’ll get into.
- Easy to find – Readily available in many varieties from numerous suppliers.
Cons:
- Machining challenges – Some steel alloys are more difficult to machine than others. Can become work hardened during some machining operations.
- Rust risk – With the exception of stainless alloys, steel can rust if it is not properly protected.
- Weight – Steel is a heavy metal, which can make it difficult to work with.
5 Popular Steel Alloys and Their Common Applications
- 440 – A stainless steel with excellent corrosion resistance often used for bearings, valve parts, and tooling.
- 420 – A stainless steel with good mechanical properties that’s well suited to knife blades and dental instruments.
- 316 – A highly corrosion-resistant steel that’s great for welded components and corrosive environments (e.g., marine parts).
- O1 – A hard, easily machinable steel often used to make drills and other cutting tools.
- D2 – A tough, high-carbon steel popular for tool and die applications requiring high wear resistance.
2. Cast Iron
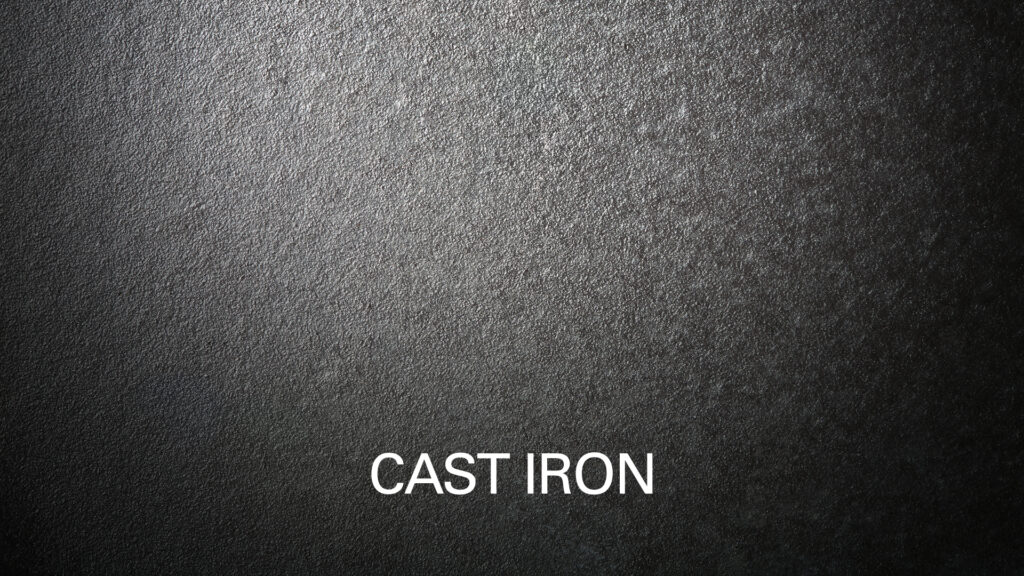
Cast iron is an alloy of iron, carbon (in higher concentration than in steel), and silicon. It’s a strong, durable material that’s relatively easy to machine. Cast iron is often used in applications where strength and durability are important, such as in engines, pumps, and valves.
Pros:
- Strength – Ideal for applications where strength is important.
- Durability – Can withstand a lot of wear and tear.
- Machinability – A good choice for projects that require precision.
- Cost-effectiveness – Relatively inexpensive, making it a good choice for projects on a budget.
- Low thermal conductivity – Cast iron’s slow absorption and gradual dispersion of heat make it an excellent material for situations where control over extreme temperatures is necessary or where uniform heat distribution is beneficial, such as in engine components or cookware.
Cons:
- Brittleness – Cast iron is a brittle material, meaning that it can break easily if it is hit or dropped.
- Highly susceptible to rust—If not properly protected during the machining process and immediately afterward, it may produce flash rust.
- Weight – Difficult to work with for some projects.
Common Applications
Cast iron has a long tradition of success in a variety of rugged applications, including engines, pumps, valves, machine tools, and cookware
3. Aluminum
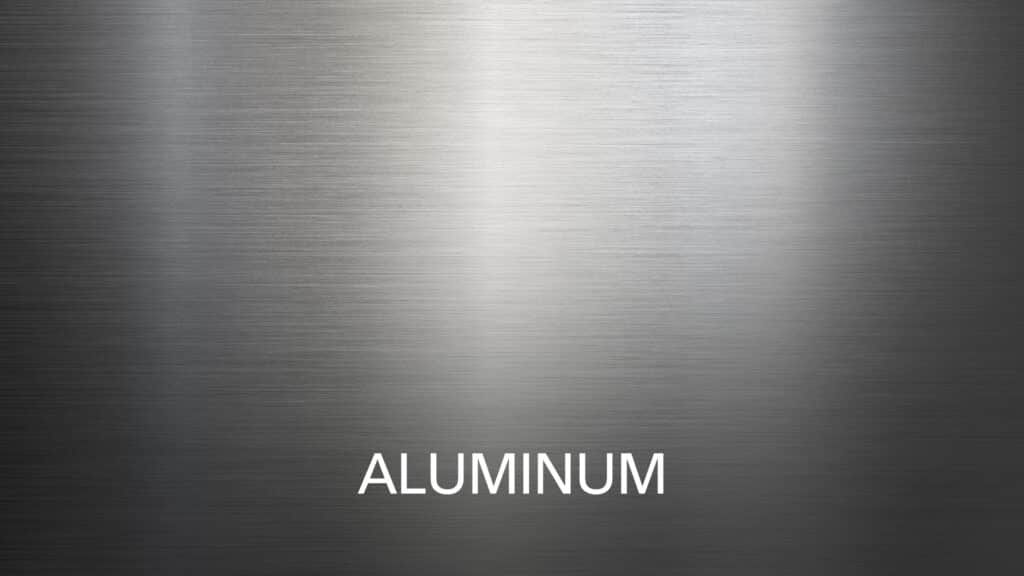
It’s good for a lot more than beer cans. Lightweight and machinable, with good corrosion resistance and electrical conductivity, aluminum is a top choice for many machining projects.
Pros:
- Lightweight—It is significantly lighter than steel, making it ideal for applications where weight reduction is essential, such as the aerospace, automotive, and transportation industries.
- Machinability – Allows for easy cutting, drilling, milling, and shaping with minimal tool wear.
- Corrosion resistance – Naturally forms a protective oxide layer when exposed to air.
- Electrical conductivity – Great for electrical and electronic applications, such as wiring, conductors, and heat sinks.
- Recyclable – An environmentally friendly choice for sustainable manufacturing practices.
Cons:
- Softness – This can lead to issues such as galling, burr formation, and poor chip control during machining.
- Low strength – Generally not as strong as steel or other metals, limiting its suitability for high-stress applications.
- High thermal conductivity – This can cause heat buildup and thermal expansion during machining, requiring careful consideration of cutting parameters and tooling.
- Challenging to finish – Tends to form gummy chips, requiring proper tool selection and machining techniques.
5 Popular Aluminum Alloys and Their Common Applications
- 6061 – A versatile alloy with good strength that’s popular for structural applications (marine hardware, bike frames).
- 7075 – A high-strength alloy beneficial for aerospace components and sporting goods.
- 6063 – An extruded alloy with good surface finish. Popular for architectural applications such as window and door frames.
- 2024 – A high-strength alloy with excellent fatigue resistance used in aircraft structures, military vehicles, and other durable components.
- 5052 – A formable, weldable alloy that’s a good choice wherever corrosion resistance is key, such as automotive panels, marine components, and kitchen appliances.
4. Titanium
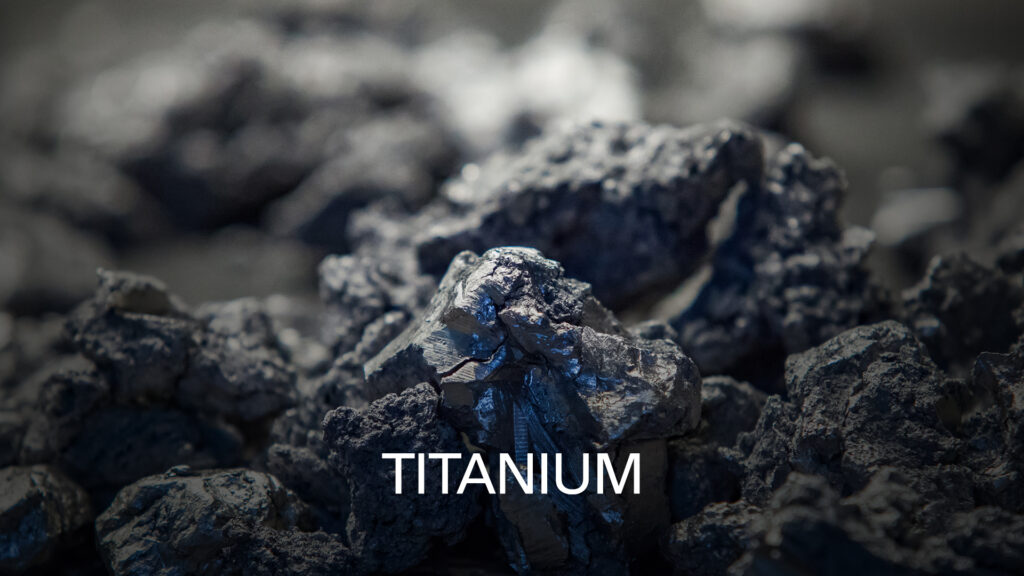
Titanium has developed quite a reputation as a premium metal for being super-strong and lightweight. And it is, so it’s common in aerospace, medical, and marine applications. But it comes at a high price tag and can be difficult to machine, limiting it to specialized, demanding applications.
Pros:
- High strength-to-weight ratio – Ideal where weight reduction is crucial, such as in the aerospace, automotive, and medical industries.
- Exceptional corrosion resistance – Even in harsh environments such as saltwater, chemical processing, and aerospace applications.
- Biocompatibility – Non-toxic, making it suitable for medical implants, prosthetics, and surgical instruments.
- High-temperature resistance – Maintains its mechanical properties at high temperatures.
- Low thermal conductivity – Reduces heat transfer during machining and helps prevent thermal distortion.
Cons:
- High cost – More expensive than many other metals, which can significantly increase material costs for machining projects.
- Low thermal conductivity – This is also sometimes a disadvantage because heat can build up and cause tool damage.
- Work hardening – Tends to harden up during machining, which can increase cutting forces, tool wear, and machining time.
- Reactive – Can react with certain materials and gasses at high temperatures, leading to weld contamination, surface discoloration, and brittleness.
- Specialized – Needs specialized tooling and cutting techniques to overcome high cutting temperatures, work hardening, and chip evacuation challenges.
5 Popular Titanium Alloys and Their Common Applications
- Grade 2 – The most common grade, with good strength and ductility for aerospace components, marine hardware, chemical processing equipment, medical implants, and prosthetics.
- Grade 5 (Ti-6Al-4V) – The most widely used titanium alloy, with excellent strength, toughness, and corrosion resistance. Great for aerospace structures, aircraft engines, turbine components, automotive parts, and sporting goods.
- Grade 7 – A corrosion-resistant titanium alloy with enhanced weldability and formability. Common in chemical processing equipment, heat exchangers, and desalination plants.
- Grade 23 (Ti-6Al-4V ELI) – A medical-grade alloy with reduced oxygen and iron. Provides excellent biocompatibility and fracture resistance in medical implants, orthopedic devices, dental implants, and surgical instruments.
- Titanium Grade 12 – Good weldability and corrosion resistance, similar to Grade 2. Suitable for chemical processing equipment, heat exchangers, and marine hardware.
5. Brass
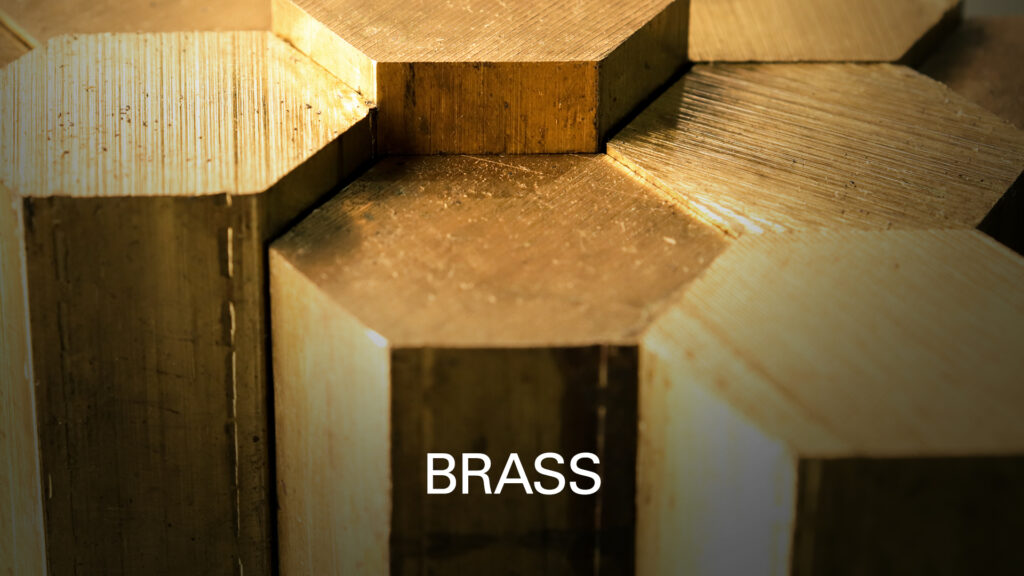
Brass is a strong, durable, and corrosion-resistant alloy of copper and zinc. Two reasons you might enjoy working with brass: It cuts easy, and it looks great. It’s a great choice whenever your project calls for a distinctive look.
Pros:
- Machinable – Easy to cut, drill, mill, and shape, with minimal tool wear. Produces fine chips and smooth surface finishes.
- Corrosion resistant – Great for outdoor and marine applications.
- Attractive – Distinctive golden-yellow color and a lustrous finish.
- Low friction – Suitable for sliding or rotating parts, such as bearings, gears, valves, and fittings.
- Antibacterial – Certain copper-rich brass alloys are helpful in healthcare, food processing, and plumbing applications.
Cons:
- Softness – Can lead to issues such as galling, burr formation, and poor chip control during machining.
- Work hardening – Especially at high cutting speeds and feeds, which can increase cutting forces and tool wear.
- Price volatility – Due to fluctuations in the cost of copper and zinc, the primary alloying elements.
- Low melting point – May not be suitable for applications requiring high temperatures.
5 Popular Brass Alloys and Their Common Applications
- C260 (aka Cartridge or 70/30) – A versatile alloy of about 70% copper and 30% zinc. Good for brass fittings, valves, plumbing fixtures, electrical components, ammunition casings, musical instruments (such as trumpets and trombones).
- C360 (aka Free-Cutting or 60/40) – A leaded alloy of about 60% copper and 40% zinc, plus a small amount of lead. Common in screws, nuts, bolts, fasteners, gears, couplings, valve stems, and architectural hardware.
- C464 Naval Brass – A high-strength brass alloy with excellent corrosion resistance in marine environments. Popular for marine hardware, shipbuilding components, propeller shafts, marine valves, pump parts, and underwater fittings.
- C693 (Silicon Bronze) – A high-strength brass alloy containing approximately 96% copper and 3% silicon. High tensile strength makes it great for architectural hardware, decorative elements, sculpture, jewelry, marine fittings, and electrical connectors.
- C485 (Leaded Commercial Bronze) – A leaded brass alloy with improved machinability and wear resistance. Used in bearings, machine parts, and valve components requiring enhanced machinability and lubricity.
6. Copper
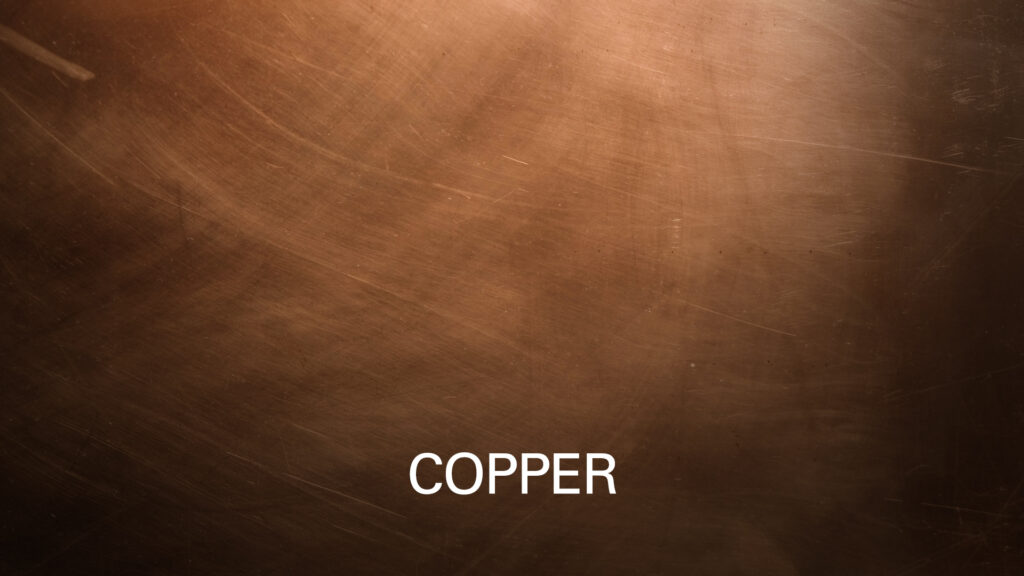
Copper is an attractive reddish-brown metal widely used in machining due to its excellent electrical conductivity, thermal conductivity, corrosion resistance, and malleability. You might choose copper whenever you need to create a quality electrical component or something decorative.
Pros:
- High electrical conductivity – Ideal for electrical and electronic applications, such as wiring, connectors, and circuit boards.
- Superior thermal conductivity – Great for heat exchangers, cooling systems, and other thermal management applications.
- Corrosion resistance – Particularly in atmospheric and freshwater environments.
- Malleability – Allows easy forming, bending, and shaping into complex geometries and intricate designs.
- Antimicrobial properties – Inhibits the growth of bacteria and fungi, making it suitable for medical and healthcare applications.
Cons:
- Softness – Can lead to issues such as galling, burr formation, and poor chip control during machining.
- Work hardening – Especially at high cutting speeds and feeds, which can increase cutting forces and tool wear.
- Oxidation – Tarnishes over time, particularly in humid and acidic environments, requiring surface treatments or protective coatings to maintain its appearance.
- Cost – Can be prohibitive depending on the size of the project.
- Lower melting point – May not be suitable for high-temperature applications.
5 Popular Copper Alloys and Their Common Applications
- C110 (aka Electrolytic Tough Pitch or ETP Copper) – A pure copper alloy with high electrical conductivity and excellent formability. Used for electrical components and conductive seals.
- C101 Oxygen-Free Copper (OFC) – A high-purity copper alloy with improved electrical conductivity and solderability. Good for high-performance electrical applications (RF connectors, audio cables).
- C12200 (aka Phosphorus Deoxidized or DHP Copper) – An alloy with small amounts of phosphorus, which acts as a deoxidizing agent. Often used for plumbing and HVAC applications.
- C145 Tellurium Copper (Free-Cutting Copper) – An alloy with small amounts of tellurium, which improves machinability and reduces chip breakage. Used in electrical connectors, switches, circuit breaker components, welding electrodes, and injection mold inserts.
- C63000 – A corrosion-resistant alloy used for chemical processing equipment and marine applications.
Bonus: Plastics
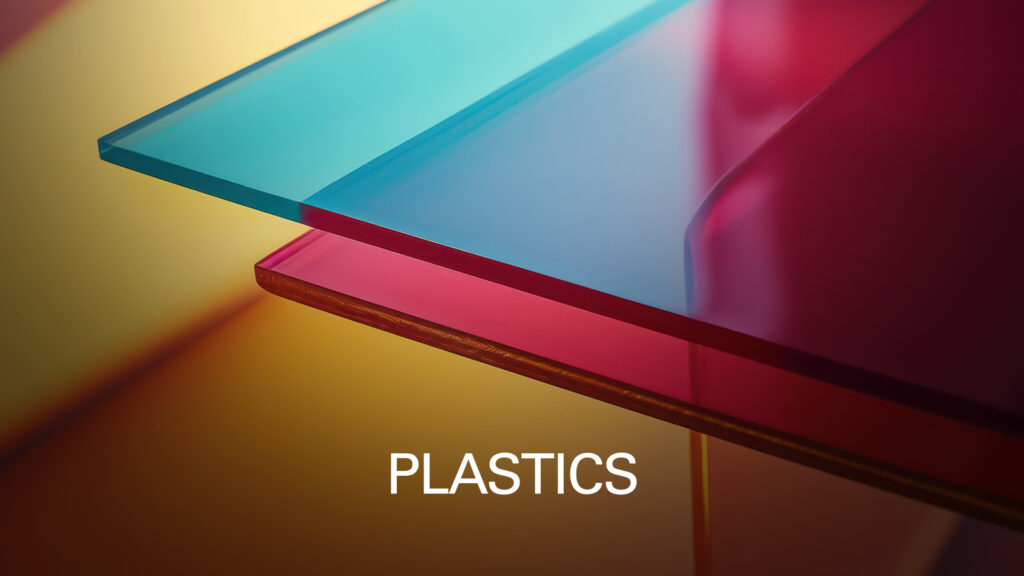
OK, so plastics aren’t metals. And you may not think of these often petroleum-based, flexible synthetic materials as being great for machining. But the truth is there are several types of plastics that are easy to cut and form into complex shapes. And plastics wouldn’t be so ubiquitous today if they didn’t work well in a wide array of applications. So sooner or later, you’ll machine some kind of plastic.
Pros:
- Lightweight – Ideal for applications where weight is a critical factor.
- Corrosion resistance – Great for use in harsh environments.
- Electrical insulation – Certain plastics are popular for electrical components.
- Chemical resistance – Certain plastics are resistant to a wide range of chemicals, making them suitable for use in chemical processing applications.
- Low cost – Plastics are generally less expensive than metals, making them a cost-effective option for machining projects.
- Machinability – Requiring less cutting force and tool wear, resulting in faster machining times and smoother surface finishes.
- Aesthetic variety – Offering a wide range of color and texture options.
Cons:
- Low dimensional stability – Exhibiting shrinkage or expansion under temperature variations, requiring care during machining and assembly.
- Flammability – Certain plastics can release toxic gasses when burned.
- UV sensitivity – Can degrade over time.
- Tool wear – May require specialized tooling and cutting techniques to avoid abrasion.
5 Popular Plastics and Their Common Applications
- Acetal (Polyoxymethylene or POM) – A tough, hard, and low-friction plastic often used for gears, bearings, and other mechanical components.
- Delrin – A type of acetal plastic with increased stiffness and fatigue resistance. Popular for gears, bearings and internal automotive components.
- ULTEM (Polyetherimide or PEI) – A high-performance plastic known for excellent electrical insulation and high-temperature resistance. Ideal for electrical connectors and semiconductors.
- Polycarbonate – A strong, tough, transparent plastic often used for lenses, windows, and other optical applications.
- PVC (Polyvinyl chloride) – A versatile plastic for pipes, fittings, and other industrial applications.
The Power to Machine Any Material
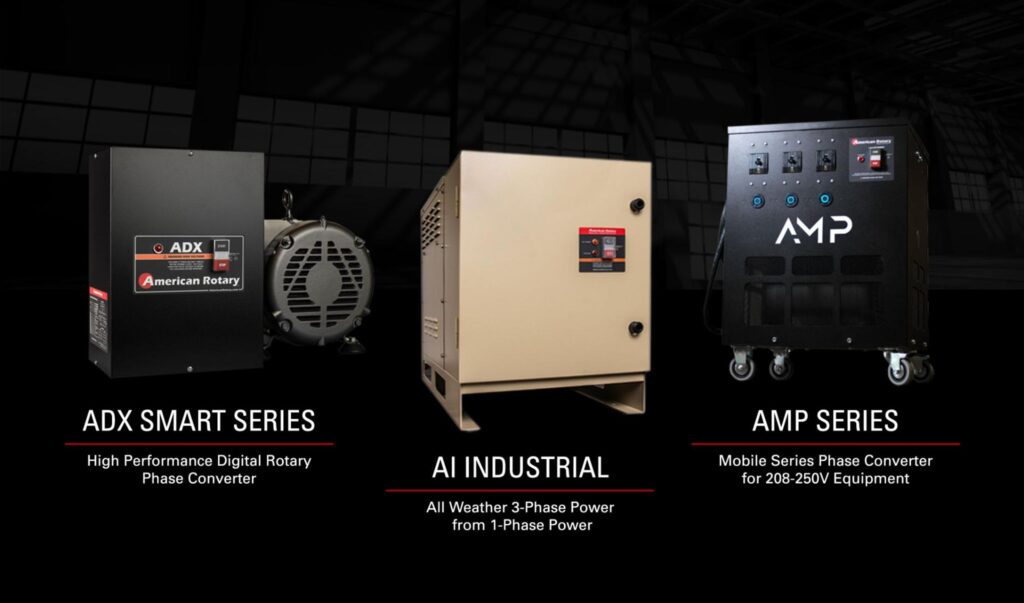
Want to be able to machine any of these materials, and more?
If so, you need to make sure you have capable machining equipment. A three-phase mill or lathe will enable smoother, more efficient cutting of all kinds of material.
You just need a way to power it. That’s where a rotary three-phase converter from American Rotary comes in. In fact, our high-quality, USA-made converters can provide balanced, efficient power for your whole shop.
Learn more about American Rotary three-phase converters for machining.