It’s precise. It’s efficient. It’s the state of the art. No wonder CNC (computer numerical control) is the platform of choice for so many types of modern manufacturing processes.
In this guide, we’re going to focus on the dynamic duo of CNC machining: turning and milling—the two most popular machines around the world. Why and when would you use either machining process? What are the key differences? We’ll look at the fundamentals in this overview.
CNC Turning
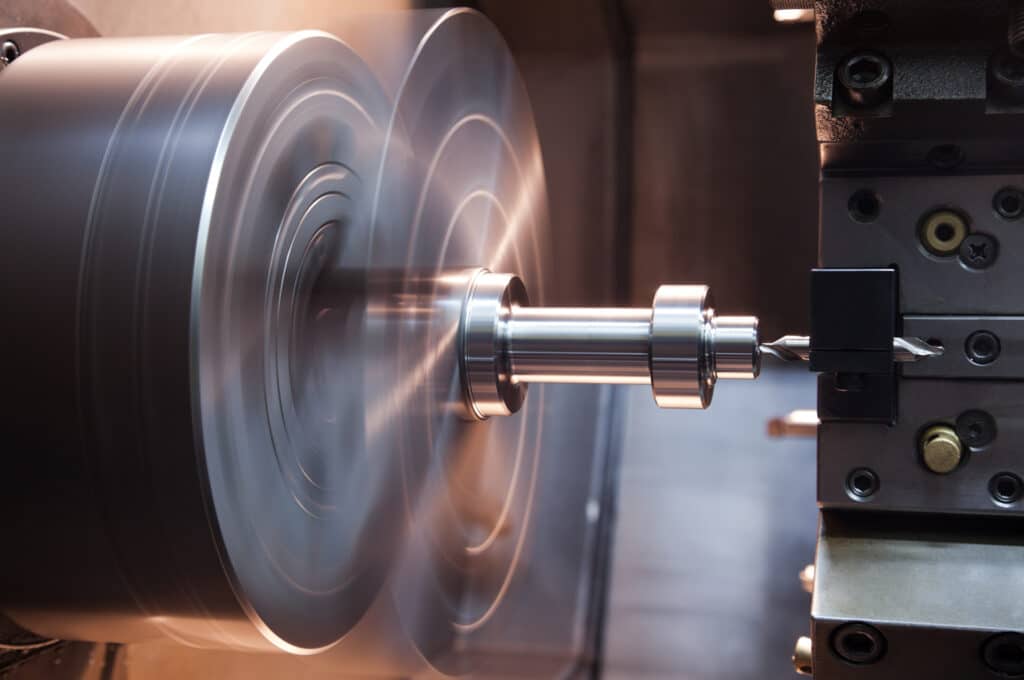
If you have some basic subtraction machining knowledge, you know that the core machining operation of turning is done on a lathe.
You can do a lot on a classic manual lathe. But for more complex shapes, tight tolerances, or high volumes, your best bet is to use a CNC lathe. Let the computer handle the hard part of guiding the tools.
In CNC turning, the lathe rotates the workpiece at high speed. Based on a CNC program, the machine feeds cutting tools against the workpiece to shape it. You can cut material from both inside and outside your workpiece. Processes include:
- Core facing
- Threading
- Boring
- Creating grooves, threads, and tapers
- Drilling center holes on turned pieces
CNC turning is ideal for creating repeatable cylindrical parts, including shafts and spindles.
CNC Milling
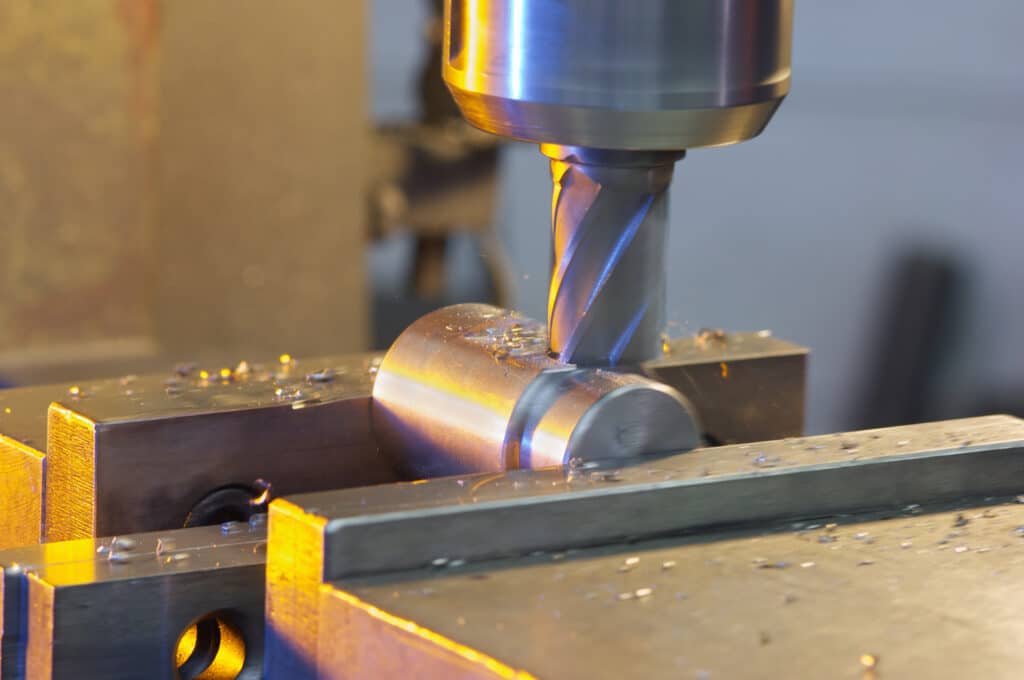
Rather than rotating the workpiece, a milling machine cuts metal by spinning a cutting tool, or spindle.
With a manual mill, you move the stationary workpiece along an axis perpendicular to the spindle axis until the two meet for cutting. As with turning, when you get into more complex shapes, precise tolerances, and high volumes, a CNC machine is the way to go.
The CNC code tells the milling machine to move the workpiece (and sometimes the tools as well) in specific directions at specific speeds. Milling processes are great for cutting:
- Intricate flat shapes
- Elaborate 3D objects
- Precise holes and slats
Get a sense of what you can do in these 10 easy CNC milling projects.
What Are the Differences Between a CNC Lathe and Mill?
On either a CNC lathe or a CNC mill, you can do most of your fundamental machining techniques at high precision.
But there’s a fundamental difference in how each cuts away raw material.
A CNC lathe applies non-rotating cutting tools to a rotating workpiece. The turning process usually involves removing material from the outer diameter of a workpiece.
Meanwhile, a CNC mill doesn’t spin the workpiece; it spins the cutting tool. It holds the tool in a tool holder in a fixed position. Or it can raise or lower the spindle against your workpiece. Then, it moves the workpiece to meet the tool.
Should You Use a CNC Mill or Lathe For Your Process?
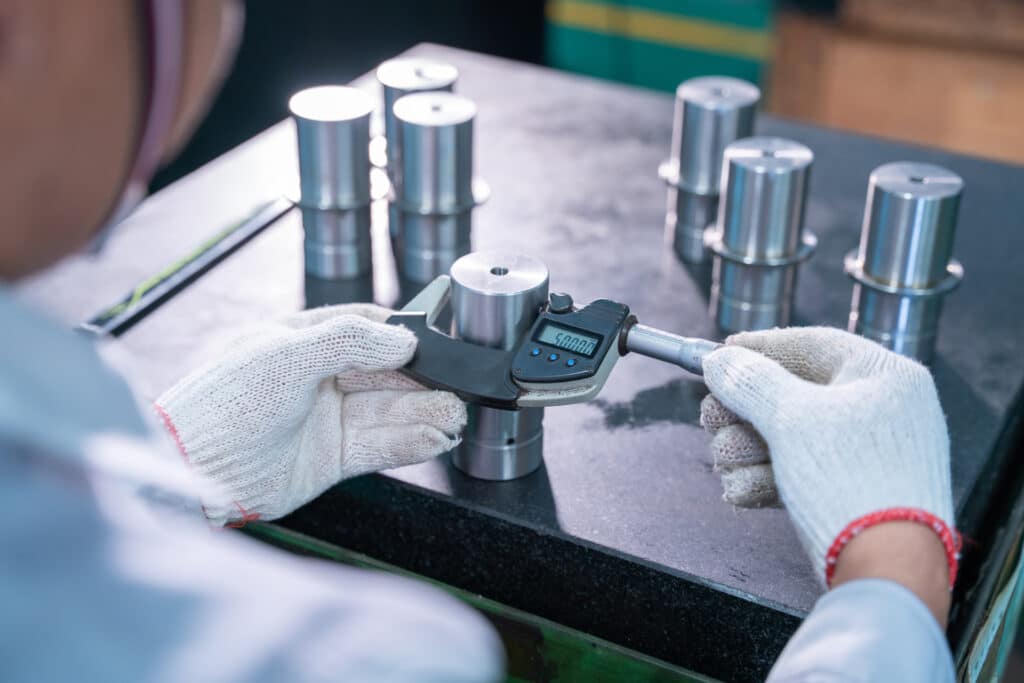
Based on the core difference in configuration, the decision on which machining method is right for you breaks down like this:
- A CNC lathe is the right choice when shaping or cutting cylindrical or symmetrical shapes.
- CNC milling is great for creating flat and irregular surfaces, boring holes, and cutting gears, grooves, and other features—but not round shapes.
Coupled with these distinct advantages, the versatility of these machines makes them must-have metalworking equipment in any machine shop.
Even better, get them working together! Many shops pair CNC turning and CNC milling next to each other. They team up well to create a wide range of complex shapes out of metal, wood, plastic, and other materials.
One Key Thing They Have in Common
To pull off the precise operations you want, both machines need strong, steady power.
Using three-phase electricity—rather than the standard single-phase electric service—will enable smoother operation. You’ll get better surface finishes, longer tooling life, and less scrap.
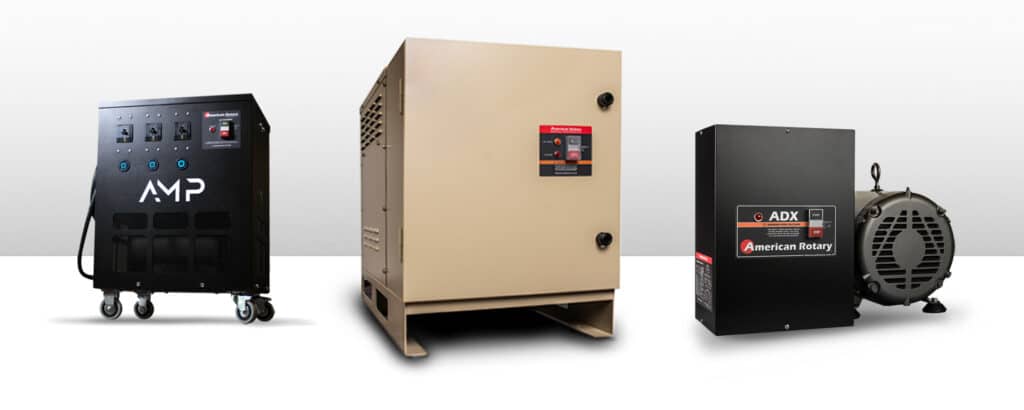
How do you get 3-phase in your shop? A USA-made American Rotary phase converter can provide all the reliable, efficient 3-phase power you need. That includes your three-phase CNC machine and any single-phase equipment, too!
Contact us today to discuss the power requirements for your shop.