If you have some machining skills and entrepreneurial aspirations, setting up a home machine shop could be a dream come true.
But of course, it’s going to cost you. Your major pieces of machining equipment can run up to several thousand dollars each, so it is worth doing your due diligence. To help you make informed decisions with your hard-earned money, this buyer’s guide will provide some advice on the most important machines.
Lathe
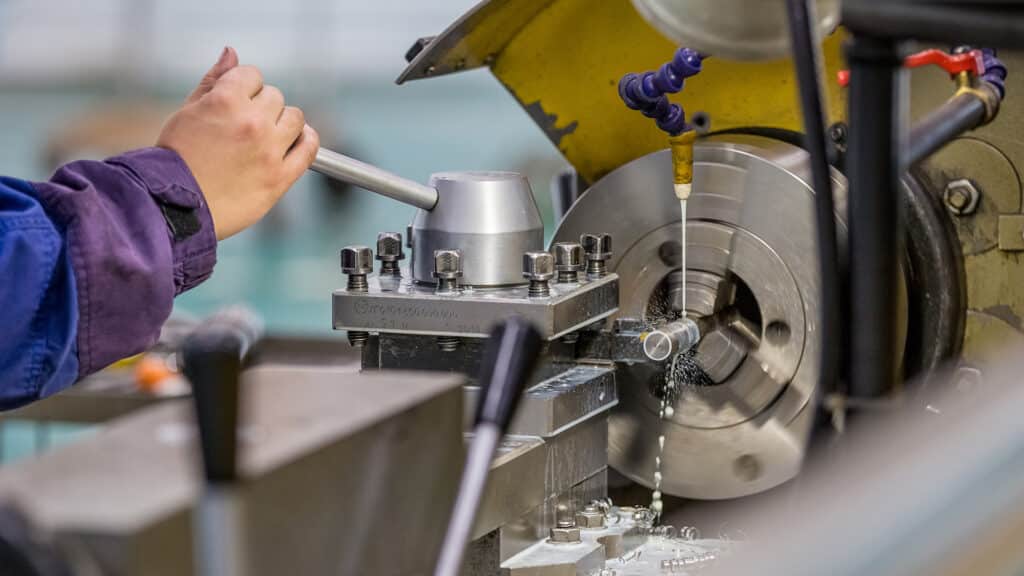
A metal lathe represents one-half of the dynamic duo (along with the next machine on this list) of your machine shop.
You’re looking at a bare minimum of $5,000 (and usually many times that) for a new, mid-size metal lathe from a reputable manufacturer like Grizzly, Jet, South Bend, or Precision Matthews.
Buying used via Facebook (there’s even a group called “Home Machine Shop SALES”), eBay, or government surplus auctions like public surplus or Municibid can save you a lot of money. But you need to do your homework on these options.
Here are a few things to look out for with any lathe:
- Bed size: Make sure it can accommodate what you envision working on. An 8×24 is a good mid-size range.
- Backlash: Every lathe will have some degree of play when changing the direction of motion. Always ask the seller about backlash so you can determine whether accounting for this issue in your projects will be worth your trouble.
- Appearance: Lathes take a beating, so you can expect significant wear. But that doesn’t mean a used lathe should look like it’s about to fall apart. Pay particular attention to bed wear closest to the spindle, where the action is.
- Maintenance history: What’s been replaced and when? No maintenance record = no deal!
Even for a used lathe, you want something big and powerful enough to realize your vision. On the low end, expect to pay at least $1,500, going up from there into several thousand dollars depending on size and condition.
Mill
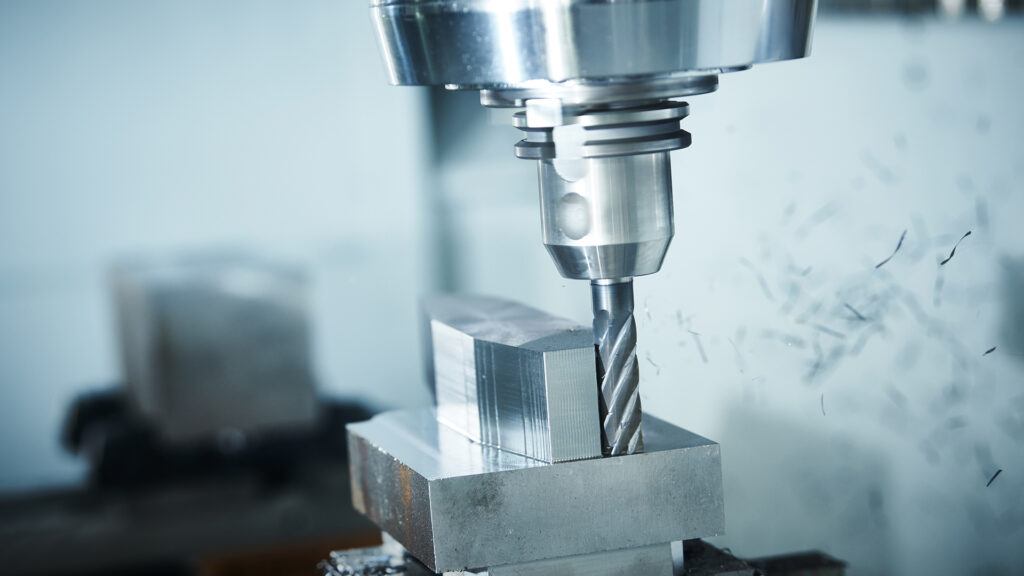
Your milling machine is the other half of the dynamic duo we mentioned above. Anything you don’t use your lathe for, you’ll be using your mill.
That level of utility comes with a price tag similar to that of your lathe. Look for reputable manufacturers such as Bridgeport, Sharp, Jet, Lagun, and Baileigh. And reserve thousands in your budget.
If you’re looking at a used mill, the same due diligence also applies. Considerations include:
- Table size: The right size for you depends on the types of projects you want to take on. But 9×49 is a good standard size that will accommodate a wide range of needs.
- Backlash: It’s not a problem unique to lathes.
- Appearance: Some wear is to be expected on a used mill, but take a close look around. Test operation before buying, too.
- Maintenance history: Related to the bullet above, the service history offers further insight into the possible future of the machine.
If you get lucky, you might find a used mill in decent shape for only a few thousand dollars. But more likely, you’re looking at $5,000+.
Tooling
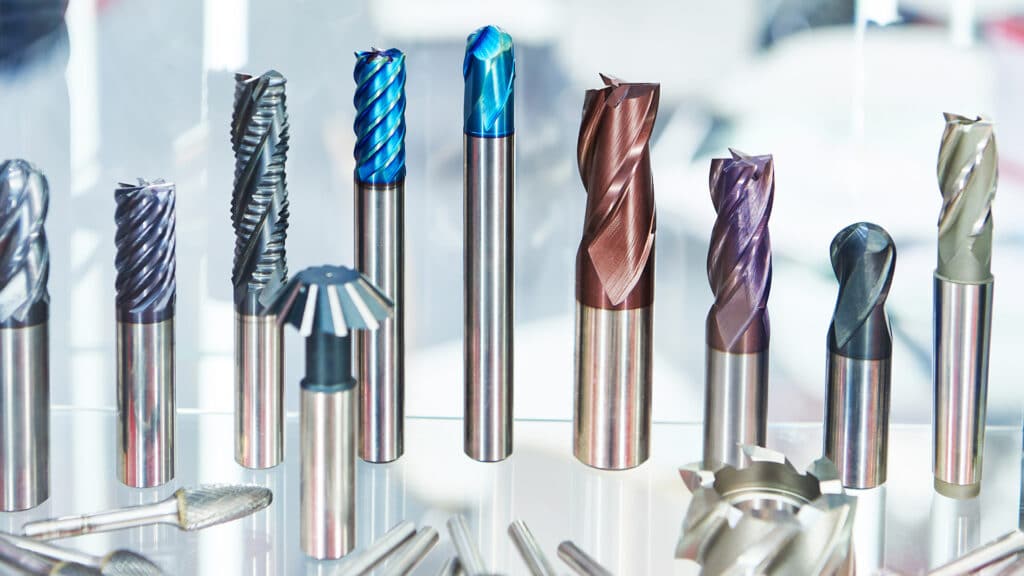
If you’re going to cut metal, you need strong tools. Resist the allure of too-cheap-to-be-true tooling you find on online or discount tool stores.
Look for machine tools made of carbide from well-known names like Walter, Kennametal, OSG, or Guhring. They won’t be cheap—$40+ per tool is common. But they’ll last longer and cause less scrap. So you’ll save money on raw stock in the long run and reduce headaches.
You can also save a bit of money by buying used, resharpened tools.
What should be in your tooling starter set?
- Lathe tools for turning
- Replaceable lathe inserts
- End mills
- Drill bits
- Mill collets for securing tools
- Taps and dies for threading
- Boring bars for enlarging holes
Total budget for tooling all in: ~$1,000
Measuring Tools
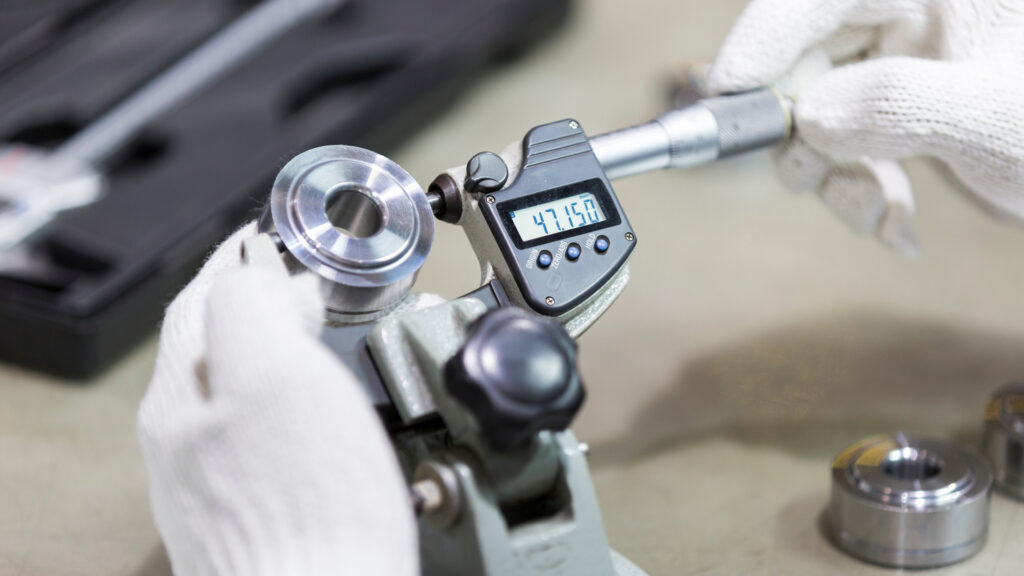
As a machinist, you know how important precision is. A full set of reliable measuring tools is essential to your success.
You’ll be using these tools daily for years. So it’s best to buy new and buy from the best. Choose reputable brands, including Brown & Sharpe, Starrett, and Mitutoyo.
Here’s a starter list:
- Calipers (at least two pairs) for measuring workpiece dimensions
- Micrometers to measure small dimensions (both inside and outside) to tight tolerances
- Dial Indicators to measure surface flatness and parallelism, as well as cutting tool alignment
- Feeler gauge set to measure small clearances
- Thread pitch gauge to check the spacing of screw threads
- Surface plate to verify flatness
- Precision squares to verify squareness
The cost of these tools can add up to $1,500 or more. But again, buying quality is worth it.
Fixturing/Tool Holders
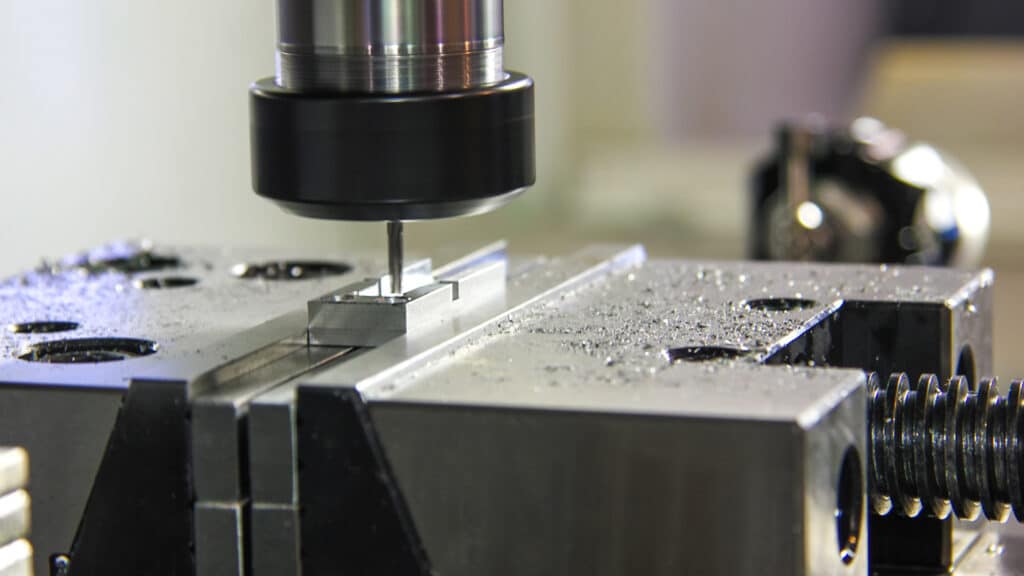
Sturdy pieces to hold your tools and workpieces steady are crucial. But you don’t need to overthink fixturing; you just need it.
Buying used is generally fine. If they’ve worked before, there’s no reason they won’t keep working, and these things don’t really wear out.
Here’s an overview of the fixturing and tool holders you’re likely to need:
- Kurt mill vise for clamping your workpiece securely
- Rotary table to rotate your workpiece for cutting at different angles
- Mill indexer, which rotates your workpiece and locks at specific positions
- Mill and lathe tool holders
- Hold-downs for securing workpieces to the table
- Lathe jaws
Total budget for tool holders and fixturing should be ~$1,500. But keep in mind you can acquire these on an as-needed basis vs. all at once.
Basic Hand Tools
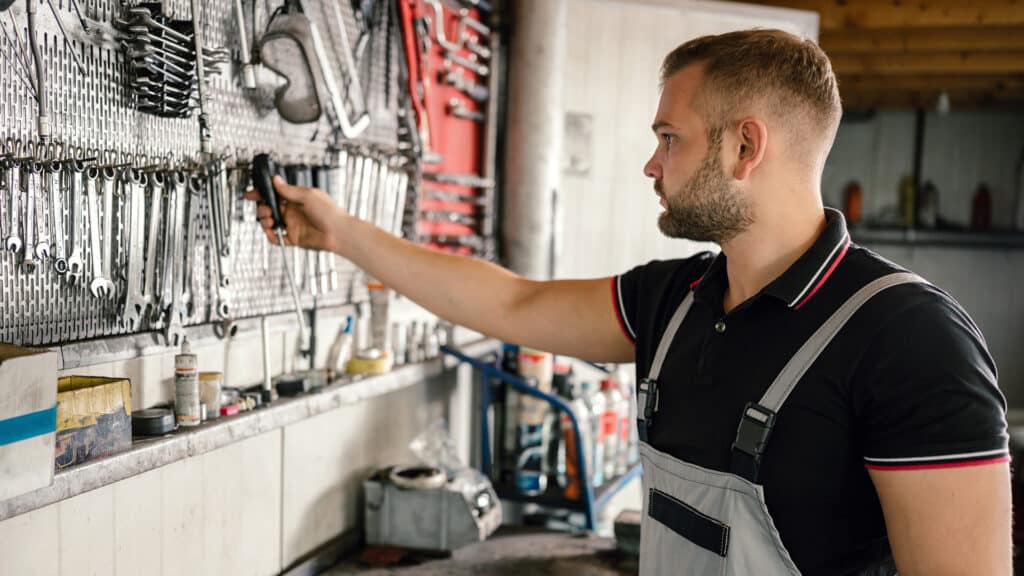
With your powerful, big-ticket items out of the way, don’t forget about the everyday stuff. You’ll need an array of hand tools for various tasks around the shop:
- Sharpening stone for deburring
- Edge finder to locate the edge of your workpiece for spindle alignment
- Wrench set in imperial and metric sizes
- Hex keys in imperial and metric sizes
- Files in a variety of shapes, sizes, and cutting styles
- Hammers, including a dead blow and brass hammer
- Center punches for hole placement
For additional ideas on tools you might want, check out our essential machining tools for beginners.
Figure your initial budget for hand tools to be $100 to $150.
Total budget for all items: $7,500 – $15,000
3-Phase Power
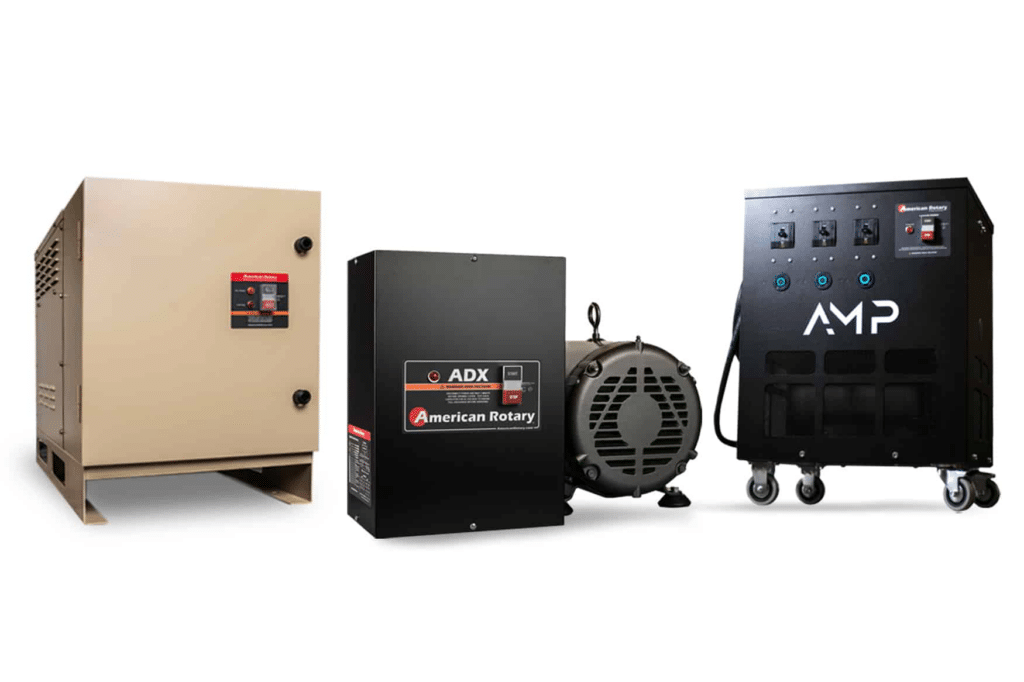
As you can see, machining is not a cheap pastime. But it’s a rewarding one! So, if you’re making the investment, you should get the toughest equipment available in your budget.
In the case of your lathe and your mill, that means machines that run on 3-phase electricity for smoother operation. You need to consider how you’ll power this equipment (because you probably have single-phase electric service at home).
Solution: A rotary three-phase converter to convert your single-phase to 3-phase.
To that end, American Rotary’s USA-made phase converters produce balanced 3-phase power to keep your whole shop running—including any single-phase equipment.
Contact us anytime for help with sizing to meet your needs.