The array of metalworking machines you can get for your home shop is amazing. But assuming you don’t have six figures to drop on your shop, you’re going to have to prioritize. Which metalworking tools are the most important? We run down the fundamentals in this overview.
Crafting a new piece of patio furniture. Shaping your own knives and tools. Building a box or frame. Building hot rods in your garage. It’s all possible with a decent, DIY metalworking shop.
There are a lot of places to find high-quality metalworking tools at an affordable price to get yourself started in your garage. The question is, where do you start?
The first thing you need to keep in mind is that metalworking can be extremely dangerous, so it’s important to keep yourself safe. Remember not to go anywhere near these machines with loose-fitting clothing or jewelry. And always remember to wear your PPE. For most work, this is as simple as a pair of safety glasses and some good leather gloves.
You’ll also need to make sure you can power the equipment. Working with metal takes some heavy-duty power tools. Metalworking shop tools often need three-phase electricity to handle the workload.
You’ll need a way to supply that three-phase power. We’ll discuss some of your options later. But first, let’s look at your fundamental tools.
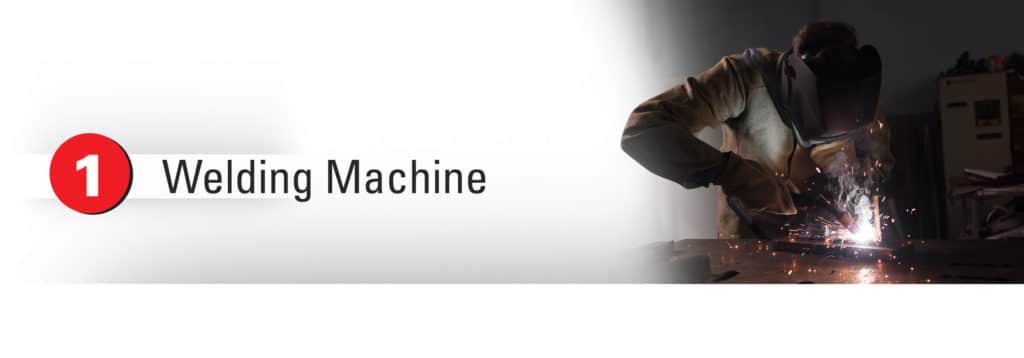
Welding Machine
Fusing two or more pieces of metal is a key capability for any metal shop.
Welding can be a challenging skill. But technological advances have made it easier for beginners and hobbyists to start in this discipline of metalwork.
If you’re new to welding, consider two types of welding machines: MIG and flux-core arc welders. While both are useful, they each have instances where one excels over the other.
A standard MIG welder is a wire-fed machine that uses argon as a shielding gas to prevent porosity. The positive side of this is that you can adjust the gas for a clean result regardless of what thickness or type of metal you are welding.
The downside is that, because the gas is being sprayed out of the nozzle, you won’t be able to use this type of machine outside or in the wind. These machines also have the added advantage of being able to weld different metals, like aluminum, since you can adjust the gas (and technique) on them.
The other type of wire feed welder is a flux core welder. The primary difference between flux core and MIG is instead of gas spraying out the nozzle, the gas is released on the burn of flux—a material inside the wire core that creates an atmosphere that protects the weld and prevents porosity.
The upsides and downsides here are the opposite of what they are for a MIG machine. While the results of a flux core welder are not as clean, you can use it outside.
The classic stick welder (aka shielded metal arc) also remains a popular option. While this is a much easier type of welding, the tradeoff is that it is messier and works only with thicker metals (down to 18 gauge vs. 26 gauge for MIG or flux-core).
The most expensive yet precise option is a TIG welder. TIG welding is an extremely difficult craft to master and takes more time. The tradeoff is that you can weld any type of metal from stainless steel to aluminum in any variety of sizes.
With all that in mind, a welder is also one of the only tools in a shop that requires specific PPE or personal protective equipment. Before you start welding, make sure you have a good helmet, leathers, and gloves. Do not try to wear flannel or fleece when welding. They are very likely to catch on fire.
Here is our picks of the best welders for various use cases.
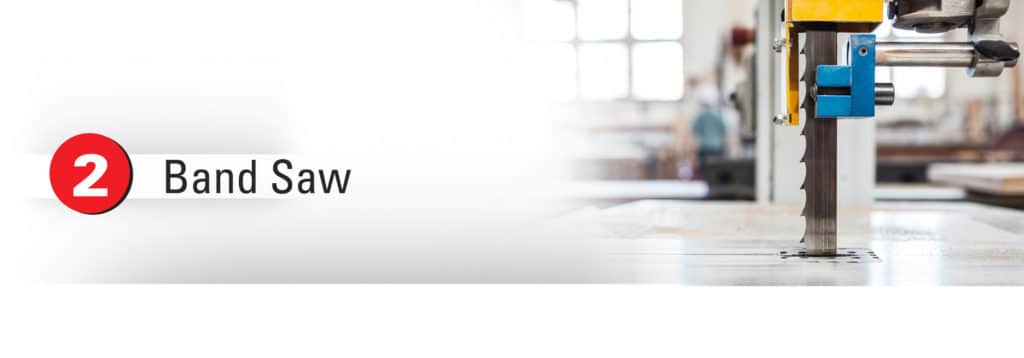
Band Saw
One of the most fundamental capabilities of a metal shop is being able to cut straight lines into metal. That makes a good band saw is another fundamental tool. It has a toothed metal blade that rotates rapidly between two wheels via a motor.
Compared to a handheld saw, a band saw is a safer way to cut through any kind of metal. It’s also easier to get clean cuts. And clean cuts are the foundation of quality work.
A metalworking band saw should include brushes to keep chips from clogging the blade. A fluid cooling system helps protect, lubricate and keep the blade clean.
Band saws come in two orientations that enable a versatile array of cuts. With a vertical band saw, you move your metal across the blade. You can do all sorts of shapes and angles this way. A horizontal band saw, on the other hand, holds your metal in place. You push the rotating blade down through the piece – good for cutting materials to length.
With all that hard work you expect your band saw to do, it pays to get a high-quality tool and blades. Check out this overview for what to look for in a metalworking band saw.
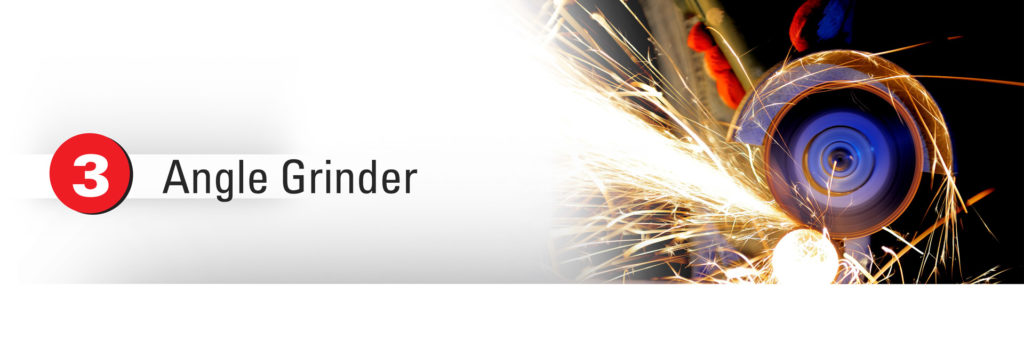
Angle Grinder
As a standalone tool, the angle grinder delivers some of the biggest bang for the buck of any metalworking tool. It’s not just for grinding down welds but also polishing and cleaning, too. They also work as a basic cutter. All in an affordable, handheld machine. This is one tool that any professional will tell you they use on a daily basis
An angle grinder features a high-speed spinning disc (up to 12,000 rpm) at a right angle to the machine. A wide array of disc attachments determine the type of work you can do. These machines also come in a range of sizes.
They’re either corded or cordless electric or pneumatic driven. Choose a corded model for more continuous work. Go cordless for greater portability.
Pneumatic angle grinders are powerful and lightweight. But the obvious drawback is you need an air compressor. The good news is that, if you have a three-phase converter, you can power a compressor that’s capable of running a pneumatic angle grinder.
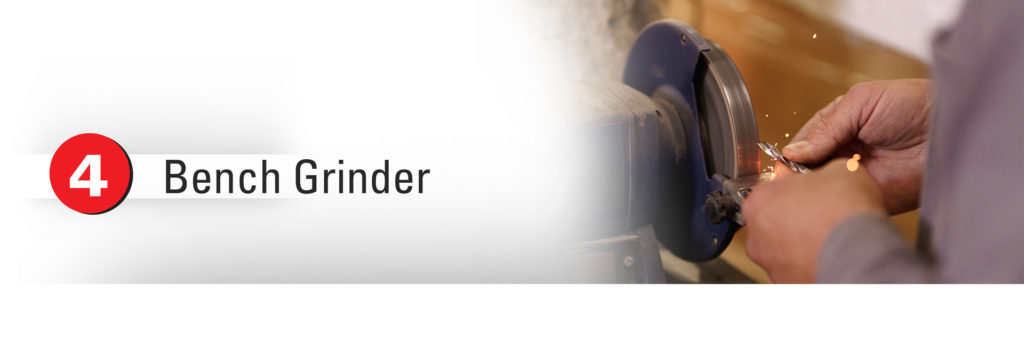
Bench Grinder
A bench grinder is a great utility tool to shape, polish, and sharpen metal. It’s as simple as it is versatile.
As the name suggests, it’s a benchtop machine. A motor spins a grinding wheel. You apply your workpiece to it to grind the piece down. A bench grinder comes with two basic wheel types: a coarse wheel for heavy-duty work and a fine wheel for smoothing.
It’s your go-to for shaping or repairing metal parts and sharpening tools.
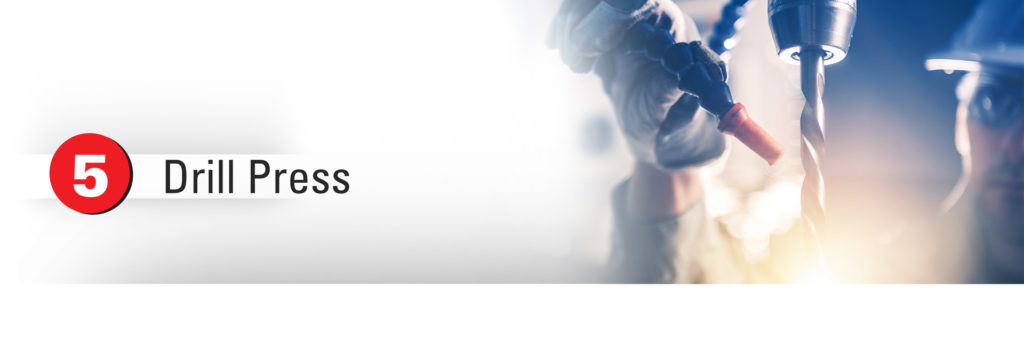
Drill Press
Why do you need a drill press if you’re skilled with a high-quality hand drill?
Two words: accuracy and repeatability.
You can drill precise holes with ease and do it the same way every time. Same size, same depth, same neat, round shape.
A drill press helps you meet consistent specs, such as drilling equidistant holes for the arms on a coat rack.
In a pinch, you can do more than drill round holes with a drill press. Change out the drill attachment to an end mill, and add a cross slide vice to turn a drill press into a makeshift milling machine. A bit of warning though, this setup will require a little patience to prevent damage to the machine, and will not be very precise.
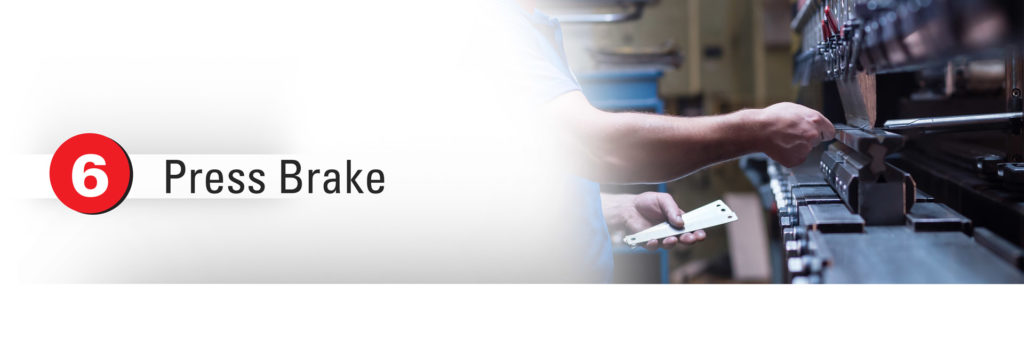
Press Brake
The last of the most common (and satisfying) tasks in a metalworking shop: bending sheet metal. Metals’ pliability is a key advantage, and a press brake is the way to do it.
We’re talking about press brakes last in this article. But you should consider your press brake early on in your shop plans. It’s likely to be the biggest and priciest piece of equipment in your shop. (However, if you’re working only with small pieces, you might consider a benchtop model.)
The basic function: You place your metal on a die, then lower a punch onto the metal to shape it. The force applied through the punch may be:
- Hydraulic: Higher force with less accuracy; more affordable
- Pneumatic: Fast but not as powerful
- Electric: Lower force with higher precision; higher upfront cost with less maintenance
- Mechanical: Force applied through a flywheel; a simpler system with some safety concerns
Your choice will depend on your budget, the types of metal you’ll be bending, and other factors. As a hobbyist, you may be able to find a simple used hydraulic system that will suit your needs. Or, if you’re ambitious and have the time, you can build your own press brake.
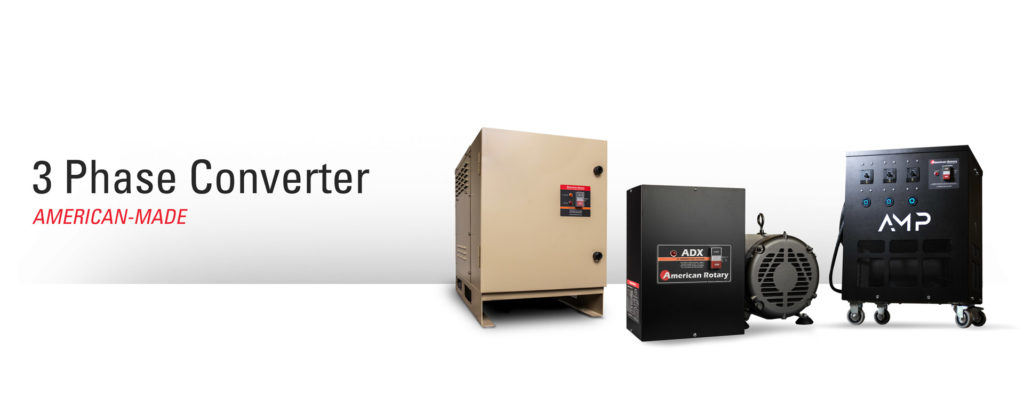
3 Phase Converter
Starting with a high-quality welder and band saw, you’ve got some great heavy-duty equipment for home metalworking. But as we mentioned earlier, these machines may need three-phase power. And you probably have single-phase electricity running to your home shop.
How can you make this work? A three-phase converter can provide reliable, efficient power.
American Rotary phase converters can power both your small and large, heavy-duty equipment. Our USA-made phase converters produce balanced 3-phase to keep your whole shop running.
Contact us anytime to discuss the power requirements for your shop. Now go make something amazing with metal.