Aluminum is a soft and ductile metal used in a wide range of applications. Should be easier to machine than harder materials, right? Not so fast, my machinist friend.
Because of aluminum’s high thermal conductivity and low melt point, you need to manage several tricky issues when machining this popular material to avoid tool damage and other frustrations. Fortunately, you can follow these 5 tips for aluminum machining to maximize efficiency.
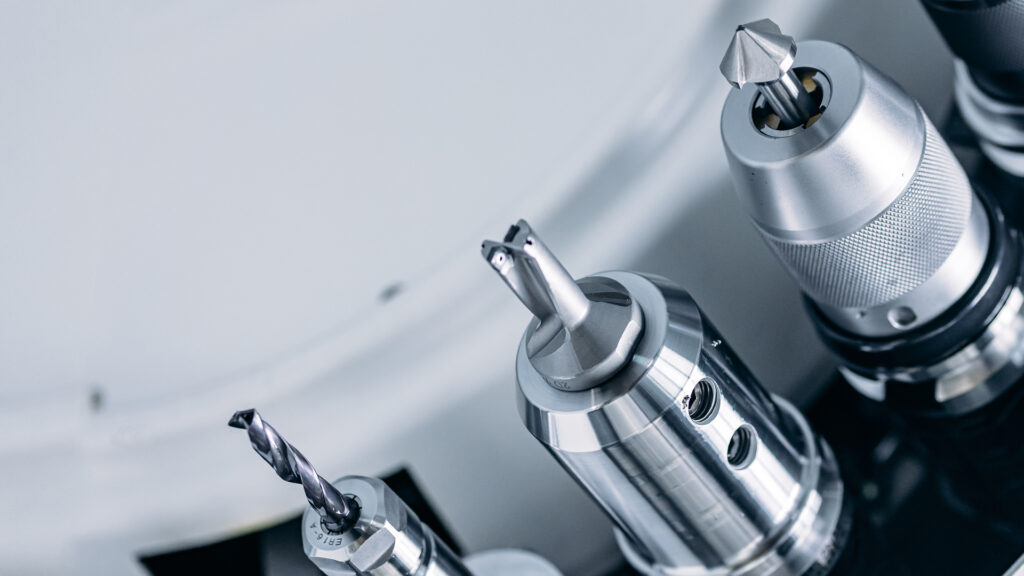
1. Use the Right Tooling
Not just any cutting tool or tool materials will do with aluminum.
It’s very ductile stuff, meaning that it tends to stretch when cut (instead of just breaking into small bits). But, the key material property to remember about aluminum is that it has a very low melting point, and when it does melt, it sticks to the cutting edge of your tooling.
To prevent these issues, you need carbide-cutting tools that can handle high RPMs while maintaining a sharp edge to keep cutting right through the metal.
In other words, choose high-hardness carbide tooling.
To minimize heat generation while still creating a good surface finish, aim for a helix angle of 35 to 45 degrees.
Cutting aluminum also creates long chips, so you want tooling that supports good chip clearance. Choose tools with a maximum of three flutes.
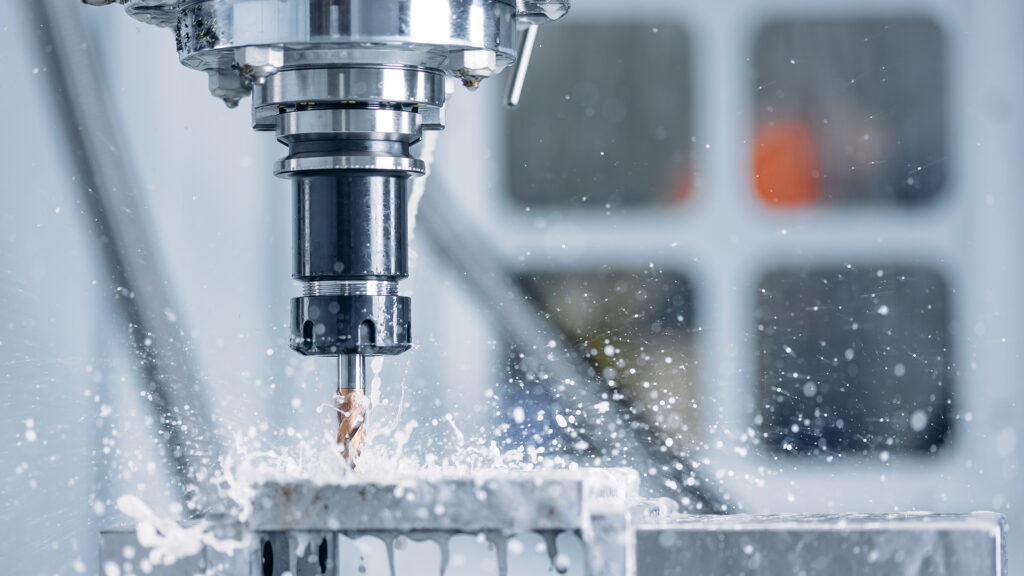
2. Use the Correct Speeds and Feeds
Considering that aluminum can melt during cutting and cause broken tools, set your machining speeds and feeds carefully.
In a conventional milling operation, high spindle speeds are advised. As for feed rate, low FPM rates can create friction that harms your tools. Conversely, fast feeds can put too much stress on your equipment.
As a result, your sweet spot will be pretty narrow, depending on the type of work (roughing, finishing, etc.), the cutter diameter, and the aluminum grade. Check with a feeds and speeds calculator or your tooling manufacturer’s charts.
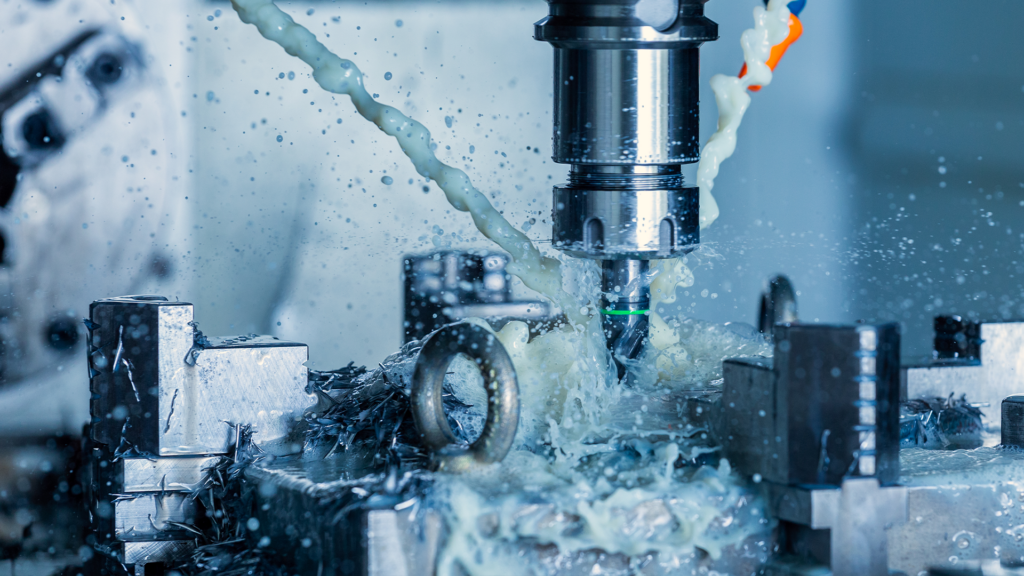
3. Maintain a Good Temperature
We say it again: cutting aluminum generates a lot of heat. You’ve got to keep things cool to prevent material softening, tool wear, poor surface finish, and other issues.
As discussed above, the proper tooling, as well as speeds and feeds, go a long way.
In addition, apply a coolant cutting fluid to the tool and the workpiece. The coolant will help dissipate heat, reduce friction, and improve chip evacuation.
Depending on your machining operation, you can use flood cooling—continuously applying the coolant—or intermittent mist cooling.
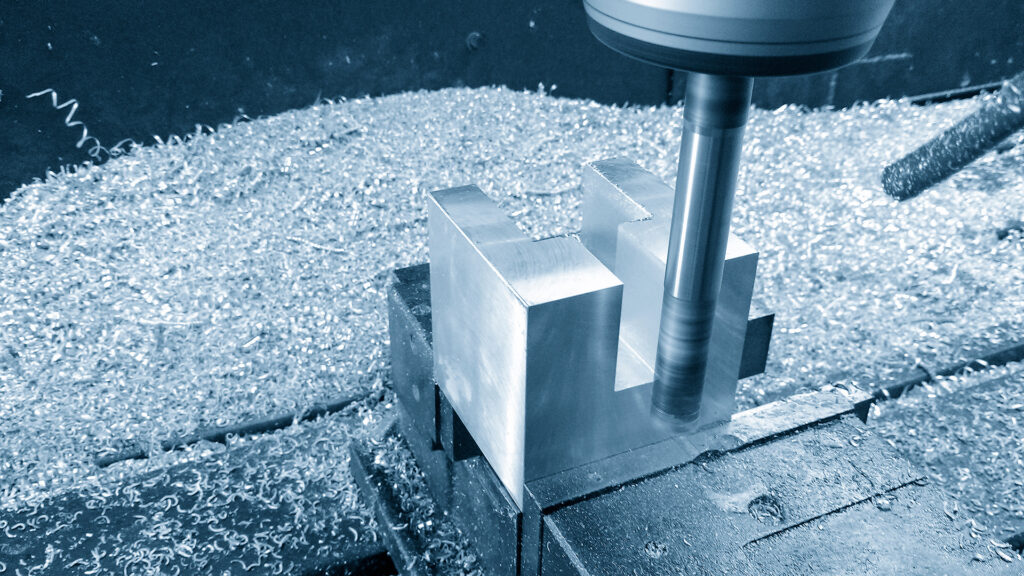
4. Watch Your Chips
Those long chips created by cutting aluminum? They can build up around your tooling and cause all kinds of problems: sticky buildup, increasing heat, and more.
Be sure to keep clearing your chips. That 3-flute maximum on the cutter will help with chip removal. So will using a cutting fluid to help flush away chips. Or consider an air blasting system to keep things clean.
Also, pay attention to the size of your chips. This is largely determined by your speeds and feeds. You want to see thinner chips that don’t look like shavings. Take this information and fine fine-tune your speeds and feeds off of it.
In any case, keep checking those chips to make sure they’re getting cleared out. Meanwhile, note the color of the chips, which may indicate various problems:
- Silver: Healthy chip formation. Good work!
- Blue or darker: Possible heat buildup. You may need to adjust your cutting parameters or use coolant.
- Red or glowing: Critical heat condition. Take immediate action to reduce heat.
- Black or smoky: Tool life is coming to an end. Check your tooling geometry and cutting parameters.
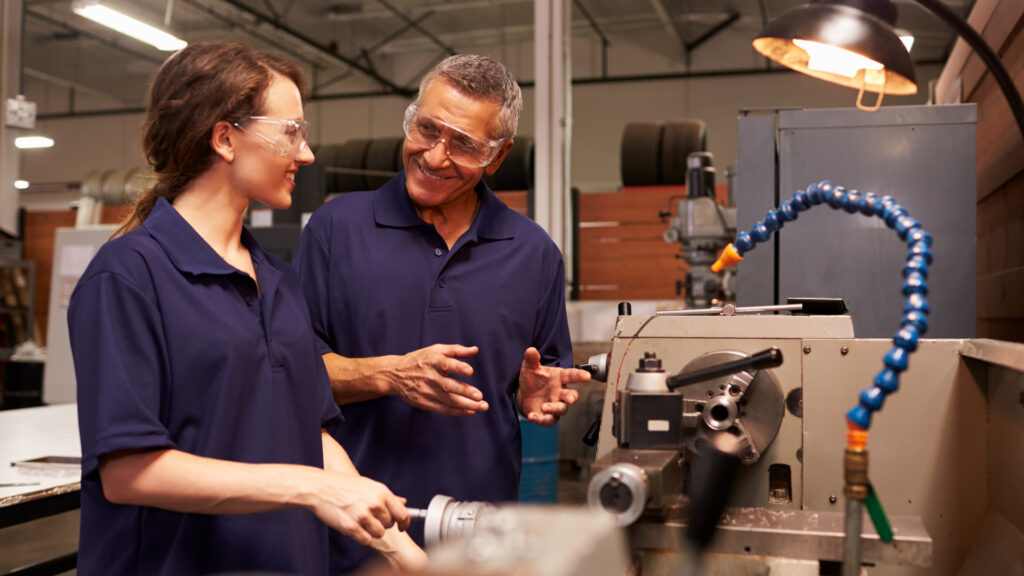
5. It Isn’t a Race
What’s the big hurry? Machining is a labor of love. Especially when cutting aluminum.
The old machinist’s saying applies: Don’t cut corners that aren’t on the print! 😉
Don’t try to make deeper cuts to save some time, as this will cause tool deflection and tool breakage. Instead, doing more shallow passes will enable better chip clearance.
Machining aluminum may be less straightforward than steel, but it’s within your grasp if you do your due diligence. Just take your time and keep all these tips in mind. And don’t hesitate to consult experienced experts if you have any questions or concerns.
The Power of Machining Aluminum
One more thing about machining aluminum: the high-quality milling machine you use is likely to need 3-phase electricity. So what do you do if your machine shop has the typical residential single-phase power service?
American Rotary’s rotary phase converters are a smart solution. One of our USA-built units can provide your shop with 3-phase power at a fraction of the cost of running a 3-phase line to your location and more efficiently than using other types of phase converters.
Contact us today to size a phase converter for the specific power requirements of your shop.